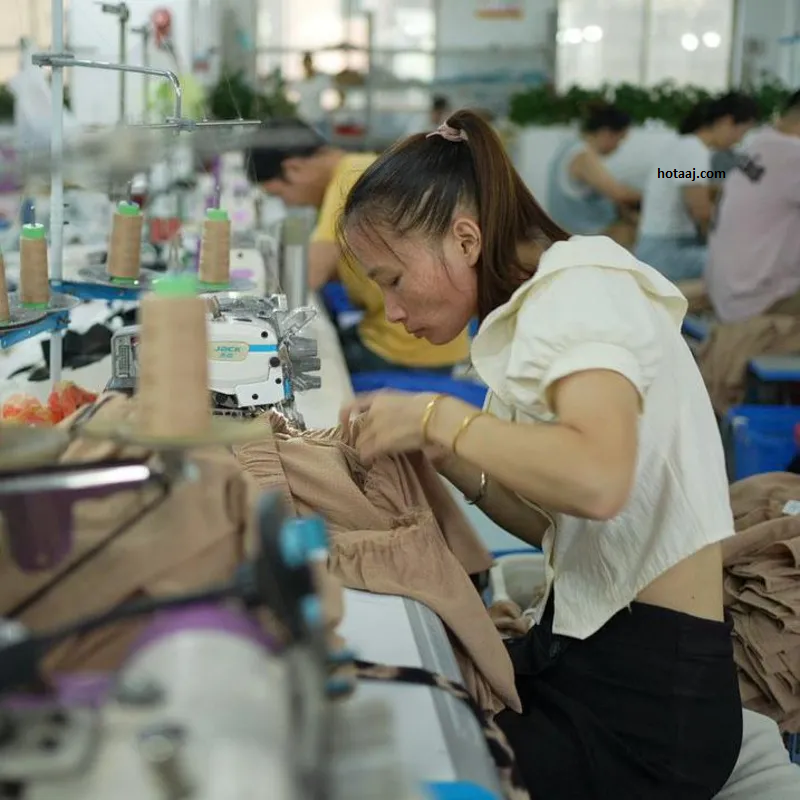
The bustling streets of Panyu, a neighborhood in Guangzhou, are home to the hum of sewing machines that define the region’s vibrant manufacturing industry. Here, factories operate around the clock, producing a vast array of garments—from t-shirts and blouses to shorts and swimwear—that will be shipped across the globe to meet the ever-growing demand for fast fashion.
This area is often referred to as the “Shein village,” as it is the center of production for Shein, the world’s largest fast fashion retailer. Shein, which was once a little-known company, has rapidly ascended to the top of the fashion world in just over five years, capitalizing on its speed and low prices. The company’s success is built on a complex network of factories and suppliers in Guangzhou, particularly in Panyu, where a relentless workforce churns out thousands of items each day.
Workers in Panyu, many of whom come from rural areas in search of better-paying jobs, endure long hours, often working up to 75 hours a week. According to reports from employees, many only have one day off each month, with no respite from the constant pressure to meet production quotas. “If there are 31 days in a month, I will work 31 days,” one worker shared with the BBC, highlighting the exhausting reality of factory life in the region.
The factories are critical to Shein’s operations, enabling the brand to offer an ever-changing collection of affordable fashion at a rapid pace. However, these working conditions raise significant concerns. The long hours and poor working conditions violate Chinese labor laws, which set limits on work hours and mandate breaks for workers. Despite these regulations, the widespread practice of overworking employees persists, reflecting the harsh realities of the global fast fashion industry.
Shein’s business model relies heavily on the efficiency and speed of its supply chain. By utilizing factories like those in Panyu, Shein can design, produce, and ship new collections to consumers worldwide in a matter of weeks—much faster than traditional fashion brands. However, this speed comes at a human cost. The workers, often underpaid and overworked, are the backbone of this global operation, but their stories remain largely unseen by the end consumers who purchase Shein’s inexpensive clothing.
In addition to its factories, Shein’s success also depends on the network of textile suppliers and labor markets that feed into its production process. The BBC’s investigation found that the working conditions in these supply chains are not unique to Shein. Guangzhou, as a major industrial hub, sees many workers enduring similar conditions across various factories and industries. Yet, Shein’s rapid rise and global reach bring the scrutiny and focus onto its operations more than ever before.
As Shein continues to grow, the questions surrounding its business practices grow louder. How much longer can the company sustain this model of low-cost, high-speed production? And, perhaps more importantly, how long will the workers in Guangzhou and other manufacturing hubs continue to bear the brunt of the pressure for affordable fashion?
Despite the increasing demand for transparency and ethical practices within the fashion industry, Shein’s practices reflect the darker side of fast fashion, where the pursuit of profit often comes at the expense of workers’ rights and well-being. The BBC’s investigation into Panyu offers a glimpse into the realities behind Shein’s success and the growing concerns over labor exploitation in the fast fashion industry. As Shein becomes a dominant player in the global market, the need for reforms and better working conditions within its supply chain becomes ever more urgent.
Shein, the privately-owned fast fashion giant, is now valued at approximately £36bn ($60bn), a testament to its incredible rise in the global fashion market. But as the company eyes a potential listing on the London Stock Exchange, its success comes with increasing scrutiny. The brand, renowned for its rock-bottom prices and lightning-fast production times, has been mired in controversy regarding its treatment of workers and allegations of forced labor, casting a shadow over its meteoric ascent.
Despite these concerns, Shein’s value continues to soar, outpacing established brands like H&M, Zara, and the UK’s Primark. This growth has largely been driven by Shein’s volume-based approach to fashion, with an inventory that runs into the hundreds of thousands and price tags that are hard to beat—£10 dresses, £6 sweaters, and prices that average under £8. These deep discounts are supported by its extensive network of suppliers, particularly in the Shein village, an area in Guangzhou, China, where about 5,000 factories work to meet the company’s insatiable demand.
However, last year, Shein faced a significant blow to its reputation when it admitted to finding children working in its factories in China, a discovery that raised questions about its labor practices. Despite this, Shein remains defiant, maintaining that it is committed to ensuring the fair and dignified treatment of all workers within its supply chain. The company issued a statement to the BBC, saying, “Shein is committed to ensuring the fair and dignified treatment of all workers within our supply chain” and emphasized its investment in governance and compliance efforts.
The company also stated that it works with auditors to ensure compliance with its code of conduct and strives to set the highest standards for pay. Yet, the long hours and poor working conditions, as reported by factory workers, tell a different story. Many laborers in the Shein village work upwards of 75 hours a week in conditions that contravene China’s labor laws, with limited days off. The demand for quick production often results in a chaotic, non-stop cycle of work, with factory doors open around the clock to accommodate endless deliveries and shipments.
The factories, once residential buildings, have been hollowed out to create makeshift production spaces, filled with sewing machines, fabric rolls, and overflowing bags of material scraps. As night falls, the pace doesn’t slow down. The workers continue laboring well past 10 PM, with trucks arriving late into the night, sometimes so packed that bolts of fabric spill onto the factory floor. These factories, integral to Shein’s model, operate under constant pressure to deliver mass-produced garments at an astonishing speed, keeping the brand’s shelves stocked and its prices low.
Despite its public statements about adhering to ethical standards, Shein’s rapid success raises important questions about the human cost of its business model. As demand for cheap, trendy clothing continues to rise, the workers in places like Shein village are left to bear the brunt of the brand’s success. The factory conditions in Guangzhou, where long hours and low wages are the norm, paint a stark contrast to the glossy image of affordable fashion sold online.
As Shein moves toward an IPO, the company’s handling of labor rights and supply chain transparency will be under intense scrutiny. Will the brand continue to prioritize speed and low costs over the well-being of its workers, or will it make meaningful changes to address the growing concerns surrounding its practices? Only time will tell, but the pressure to balance profit with ethical responsibility is mounting for this global fashion behemoth.

In the industrial heart of Guangzhou, the constant hum of sewing machines and the relentless pace of garment production form the backbone of Shein’s success. But behind the glossy online ads and rock-bottom prices lies a harsh reality for the workers powering this fast fashion empire.
A 49-year-old migrant worker from Jiangxi, who declined to share her name, describes her typical workday. “We usually work 10, 11, or 12 hours a day,” she says. “On Sundays, we work around three hours less.” She, like many others in Panyu, the district known as the “Shein village,” is part of the vast, often invisible, labor force that fuels the global supply chain of the fashion giant.
The factory where she works is part of a sprawling network of contracted garment producers. Some factories are small, others are large, but all are dependent on the whims of the fashion market. When a product becomes popular, like a pair of chinos, the demand increases, and so too does the production. Factories hire temporary workers to fulfill orders that their permanent staff cannot meet.
In an alleyway lined with bulletin boards, workers gather each day to browse job listings, assessing job opportunities and wages. It’s here that the migrant worker from Jiangxi is looking for a short-term contract, hoping to find enough work to send money back to her children, who live with their grandparents. “We earn so little. The cost of living is now so high,” she admits, her voice tinged with resignation.
She explains the pay structure: workers earn based on the number of items they produce. For simpler garments like t-shirts, the pay is about one to two yuan (less than a dollar) per piece. “I can make around a dozen in an hour,” she says, calculating the potential earnings for each task. The workers carefully inspect garments, like the chinos hanging on the bulletin board, as they determine which items are worth their time. Stitching quality and item complexity directly impact their earnings, as each garment carries a different pay rate based on its level of difficulty.
Panyu, a district that feels like the industrial lifeblood of Shein, pulses with the activity of these workers. In the mornings, the alleys fill with people hurrying to work or rushing to grab a bite from local street vendors offering dumplings, soybean milk, and eggs. Scooters whiz by, transporting workers to the factories where their labor will contribute to the endless cycle of garment production that fuels Shein’s rapid turnaround of trendy clothes.
The conditions are far from glamorous. Workers like the one from Jiangxi endure long hours in factories where their wages are tied to the speed and quantity of their output, rather than an hourly rate or standard pay. Temporary workers, often migrants from rural areas, form the backbone of this system, which has allowed Shein to create an immense inventory of inexpensive clothing and deliver it to consumers at breakneck speed.
This informal labor market, in the alleys of Panyu, represents just one facet of Shein’s extensive, yet opaque, supply chain. The low wages, long hours, and reliance on temporary workers are critical to maintaining the cost structure that allows Shein to dominate the global fast fashion landscape. However, as Shein continues to expand, questions about the sustainability of such practices and their impact on workers’ lives become more pressing.
Courtesy: ABC News (Australia)
References
- ^ National Geographic Family Reference Atlas of the World. Washington, D.C.: National Geographic Society (U.S.). 2006. p. 264.
- ^ Jump up to:a b c “World Population Prospects 2022”. United Nations Department of Economic and Social Affairs, Population Division. Retrieved 17 July 2022.
- ^ Jump up to:a b c “World Population Prospects 2022: Demographic indicators by region, subregion and country, annually for 1950-2100” (XSLX) (“Total Population, as of 1 July (thousands)”). United Nations Department of Economic and Social Affairs, Population Division. Retrieved 17 July 2022.
- ^ “GDP PPP, current prices”. International Monetary Fund. 2022. Archived from the original on 22 January 2021. Retrieved 16 January 2022.
- ^ “GDP Nominal, current prices”. International Monetary Fund. 2022. Archived from the original on 25 February 2017. Retrieved 16 January 2022.
- ^ “Nominal GDP per capita”. International Monetary Fund. 2022. Archived from the original on 11 January 2020. Retrieved 16 January 2022.
- ^ Johnson, Todd M.; Crossing, Peter F. (14 October 2022). “Religions by Continent”. Journal of Religion and Demography. 9 (1–2): 91–110. doi:10.1163/2589742x-bja10013. ISSN 2589-7411. Archived from the original on 1 August 2023. Retrieved 4 August 2023.
- ^ “Asia noun”. Oxford Learner’s Dictionaries. Archived from the original on 22 March 2022. Retrieved 16 February 2023.
- ^ “Asia Definition & Meaning”. Merriam Webster. Archived from the original on 16 February 2023. Retrieved 16 February 2023.
- ^ “Asia: The largest continent on Earth”. BBC Bitesize. Archived from the original on 7 October 2022.
- ^ Jump up to:a b Boudreau, Diane; McDaniel, Melissa; Sprout, Erin; Turgeon, Andrew. Evers, Jeannie; West, Kara (eds.). “Asia: Physical Geography”. National Geographic Society. Crooks, Mary; Gunther, Tim; Wynne, Nancy. Archived from the original on 30 June 2022. Retrieved 4 February 2023.
- ^ “The World at Six Billion”. UN Population Division. Archived from the original on 5 March 2016, “Table 2” (PDF). Archived from the original (PDF) on 1 January 2016.
- ^ “Asia Population 2022 (Demographics, Maps, Graphs)”. World Population Review. Archived from the original on 21 February 2022. Retrieved 21 February 2022.
- ^ “Population of Asia. 2019 demographics: density, ratios, growth rate, clock, rate of men to women”. populationof.net. Archived from the original on 14 July 2019. Retrieved 2 June 2019.
- ^ Jump up to:a b National Geographic Atlas of the World (7th ed.). Washington, D.C.: National Geographic. 1999. ISBN 978-0-7922-7528-2. “Europe” (pp. 68–69); “Asia” (pp. 90–91): “A commonly accepted division between Asia and Europe is formed by the Ural Mountains, Ural River, Caspian Sea, Caucasus Mountains, and the Black Sea with its outlets, the Bosporus and Dardanelles.”
- ^ Nalapat, M. D. “Ensuring China’s ‘Peaceful Rise'”. Archived from the original on 10 January 2010. Retrieved 22 January 2016.
- ^ Jump up to:a b Dahlman, Carl J; Aubert, Jean-Eric. China and the Knowledge Economy: Seizing the 21st century. WBI Development Studies. World Bank Publications. Accessed 30 January 2008. Eric.ed.gov. 2000. ISBN 978-0-8213-5005-8. Archived from the original on 4 March 2008. Retrieved 1 June 2010.
- ^ “The Real Great Leap Forward”. The Economist. 30 September 2004. Archived from the original on 27 December 2016.
- ^ “Like herrings in a barrel”. The Economist. No. Millennium issue: Population. 23 December 1999. Archived from the original on 4 January 2010.
- ^ “Suez Canal: 1250 to 1920: Middle East”. Cultural Sociology of the Middle East, Asia, & Africa: An Encyclopedia. Sage Publications, Inc. 2012. doi:10.4135/9781452218458.n112. ISBN 978-1-4129-8176-7. S2CID 126449508.
- ^ Slomp, Hans (26 September 2011). Europe, A Political Profile: An American Companion to European Politics (Illustrated, revised ed.). ABC-CLIO (published 2011). ISBN 978-0313391828.
- ^ Histories 4.38. C.f. James Rennell, The Geographical System of Herodotus Examined and Explained, Volume 1, Rivington 1830, p. 244.
- ^ according to Strabo (Geographica 11.7.4) even at the time of Alexander, “it was agreed by all that the Tanais river separated Asia from Europe” (ὡμολόγητο ἐκ πάντων ὅτι διείργει τὴν Ἀσίαν ἀπὸ τῆς Εὐρώπης ὁ Τάναϊς ποταμός; c.f. Duane W. Roller, Eratosthenes’ Geography, Princeton University Press, 2010, ISBN 978-0-691-14267-8, Eratosthenes (24 January 2010). p. 57. Princeton University Press. ISBN 978-0-691-14267-8. Archived from the original on 26 March 2022. Retrieved 21 January 2020.)
- ^ W. Theiler, Posidonios. Die Fragmente, vol. 1. Berlin, Germany: De Gruyter, 1982, fragm. 47a.
- ^ I. G. Kidd (ed.), Posidonius: The commentary, Cambridge University Press, 2004, ISBN 978-0-521-60443-7, Posidonius (1989). p. 738. Cambridge University Press. ISBN 978-0-521-60443-7. Archived from the original on 1 August 2020. Retrieved 21 January 2020.
- ^ Geographia 7.5.6 (ed. Nobbe 1845, Ptolomeo, Claudio (1845). “vol. 2”. Archived from the original on 24 May 2020. Retrieved 21 January 2020., p. 178). Καὶ τῇ Εὐρώπῃ δὲ συνάπτει διὰ τοῦ μεταξὺ αὐχένος τῆς τε Μαιώτιδος λίμνης καὶ τοῦ Σαρματικοῦ Ὠκεανοῦ ἐπὶ τῆς διαβάσεως τοῦ Τανάϊδος ποταμοῦ. “And [Asia] is connected to Europe by the land-strait between Lake Maiotis and the Sarmatian Ocean where the river Tanais crosses through.”
- ^ Jump up to:a b Lineback, Neal (9 July 2013). “Geography in the News: Eurasia’s Boundaries”. National Geographic. Archived from the original on 8 May 2016. Retrieved 9 June 2016.
- ^ Lewis & Wigen 1997, pp. 27–28.
- ^ Jump up to:a b Simpson, George Gaylord (1977). “Too Many Lines; The Limits of the Oriental and Australian Zoogeographic Regions”. Proceedings of the American Philosophical Society. 121 (2). American Philosophical Society: 107–120. ISSN 0003-049X. JSTOR 986523. Retrieved 11 June 2024.
- ^ Kealy, Shimona; Louys, Julien; o’Connor, Sue (2015). “Islands under the sea: a review of early modern human dispersal routes and migration hypotheses through Wallacea”. The Journal of Island and Coastal Archaeology. 11 (3): 364–84. doi:10.1080/15564894.2015.1119218. ISSN 1556-4894. S2CID 129964987.
- ^ New, T. R. (2002). “Neuroptera of Wallacea: a transitional fauna between major geographical regions” (PDF). Acta Zoologica Academiae Scientiarum Hungaricae. 48 (2): 217–227.
- ^ “Jejak Pembauran Melanesia dan Austronesia”. National Geographic (in Indonesian). 26 November 2015. Retrieved 11 June 2024.
- ^ Lewis & Wigen 1997, pp. 170–173.
- ^ Danver, Steven L. (2015). Native Peoples of the World: An Encyclopedia of Groups, Cultures and Contemporary Issues. Taylor & Francis. p. 185. ISBN 978-1317464006. Archived from the original on 4 April 2023. Retrieved 23 April 2022.
- ^ Wallace, Alfred Russel (1879). Australasia. The University of Michigan. p. 2. Archived from the original on 30 July 2022. Retrieved 12 March 2022.
Oceania is the word often used by continental geographers to describe the great world of islands we are now entering upon […] This boundless watery domain, which extends northwards of Behring Straits and southward to the Antarctic barrier of ice, is studded with many island groups, which are, however, very irregularly distributed over its surface. The more northerly section, lying between Japan and California and between the Aleutian and Hawaiian Archipelagos is relived by nothing but a few solitary reefs and rocks at enormously distant intervals.
- ^ Kohlhoff, Dean (2002). Amchitka and the Bomb: Nuclear Testing in Alaska. University of Washington Press. p. 6. ISBN 978-0295800509. Archived from the original on 17 May 2023. Retrieved 12 March 2022.
The regional name of the Pacific Islands is appropriate: Oceania, a sea of islands, including those of Alaska and Hawaii. The Pacific Basin is not insignificant or remote. It covers one third of the globe’s surface. Its northern boundary is the Aleutian Islands chain. Oceania virtually touches all of the Western Hemisphere.
- ^ Flick, Alexander Clarence (1926). Modern World History, 1776-1926: A Survey of the Origins and Development of Contemporary Civilization. A.A. Knopf. p. 492. Archived from the original on 30 July 2022. Retrieved 10 July 2022.
- ^ Henderson, John William (1971). Area Handbook for Oceania. U.S. Government Printing Office. p. 5. Archived from the original on 6 April 2023. Retrieved 11 March 2022.
- ^ Lewis & Wigen 1997, pp. 7–9.
- ^ “Asia”. AccessScience. McGraw-Hill. Archived from the original on 27 November 2011. Retrieved 26 July 2011.
- ^ Schwartz, Benjamin (December 2008). “Geography Is Destiny”. The Atlantic. Archived from the original on 30 September 2009.
- ^ McMahon, Gregory (2011). “The Land and Peoples of Anatolia through Ancient Eyes”. In Steadman, Sharon; McMahon, Gregory (eds.). The Oxford Handbook of Ancient Anatolia. Oxford University Press. p. 21. doi:10.1093/oxfordhb/9780195376142.013.0002.
- ^ Bossert, Helmut T., Asia, Istanbul, 1946.
- ^ Rose, Charles Brian (2013). The Archaeology of Greek and Roman Troy. Cambridge University Press. pp. 108–109. ISBN 978-0-521-76207-6.
- ^ Ventris & Chadwick 1973, pp. 410, 536.
- ^ Collins, Billie Jean; Bachvarova, Mary R.; Rutherford, Ian (28 March 2010). Anatolian Interfaces: Hittites, Greeks and their Neighbours. Oxbow Books. p. 120. ISBN 978-1-78297-475-8. Archived from the original on 4 December 2022. Retrieved 7 March 2023.
assuwa pylos “aswia” = Linear B A-si-wi-ja
- ^ Book IV, Article 45.
- ^ “Asie”. Encyclopedia: Greek Gods, Spirits, Monsters. Theoi Greek Mythology, Exploring Mythology in Classical Literature and Art. 2000–2011. Archived from the original on 4 June 2010.
- ^ Μ95, Π717.
- ^ Β461.
- ^ Liddell, Henry George; Scott, Robert; Jones, Henry Stuart; McKenzie, Roderick (2007) [1940]. “Ἀσία”. A Greek-English Lexicon. Medford: Perseus Digital Library, Tufts University. Archived from the original on 27 April 2011.
- ^ “Asia – Origin and meaning of Asia by Online Etymology Dictionary”. Etymonline.com. Archived from the original on 25 May 2017. Retrieved 9 November 2017.
- ^ Lee, Adela C. Y. “Ancient Silk Road Travellers”. Silk-road.com. Silkroad Foundation. Archived from the original on 8 November 2017. Retrieved 9 November 2017.
- ^ “How Islam Spread Throughout the World”. Yaqeen Institute for Islamic Research. Retrieved 8 August 2024.
- ^ “Did you know?: The Spread of Islam in Southeast Asia through the Trade Routes | Silk Roads Programme”. en.unesco.org. Retrieved 8 August 2024.
- ^ Ping-ti Ho. “An Estimate of the Total Population of Sung-Chin China”, in Études Song, Series 1, No. 1, (1970). pp. 33–53.
- ^ “History – Black Death”. BBC. 17 February 2011. Archived from the original on 5 June 2012.
- ^ “Christopher Columbus Quest to Reach Asia”. HISTORY CRUNCH – History Articles, Biographies, Infographics, Resources and More. Retrieved 8 November 2024.
- ^ Hu-DeHart, Evelyn; López, Kathleen (2008). “Asian Diasporas in Latin America and the Caribbean: An Historical Overview”. Afro-Hispanic Review. 27 (1): 9–21. ISSN 0278-8969.
- ^ “The Story of India”. www.pbs.org. PBS. Retrieved 8 August 2024.
- ^ Sen, Sailendra Nath (2010). An Advanced History of Modern India. Macmillan India. p. 11. ISBN 978-0-230-32885-3. Archived from the original on 22 April 2020.
- ^ “How India’s Economy Will Overtake the U.S.’s”. Time. 28 July 2023. Archived from the original on 31 August 2023. Retrieved 31 August 2023.
- ^ “Behind the Enduring Relevance of the Suez Canal Is the Long Shadow of European Colonialism”. The Wire. Retrieved 9 August 2024.
- ^ “Milestones: 1830–1860 – Office of the Historian”. history.state.gov. Archived from the original on 31 August 2023. Retrieved 31 August 2023.
- ^ “Opinion | For China, the history that matters is its ‘century of humiliation'”. South China Morning Post. 28 September 2021. Archived from the original on 31 August 2023. Retrieved 31 August 2023.
- ^ “Southeast Asia, 1800–1900 A.D.” The Met’s Heilbrunn Timeline of Art History. Metropolitan Museum of Art. Archived from the original on 31 August 2023. Retrieved 31 August 2023.
- ^ “Introduction: Race and Empire in Meiji Japan”. The Asia–Pacific Journal: Japan Focus. 15 October 2020. Archived from the original on 31 August 2023. Retrieved 31 August 2023.
- ^ Huffman, James L. (2019). The Rise and Evolution of Meiji Japan. Amsterdam University Press. doi:10.2307/j.ctvzgb64z. ISBN 978-1-898823-94-0. JSTOR j.ctvzgb64z. S2CID 216630259. Archived from the original on 31 August 2023. Retrieved 31 August 2023.
- ^ “The United States and the Opening to Japan, 1853”.
- ^ Yakoubi, Myriam (4 January 2022). “The French, the British and their Middle Eastern Mandates (1918-1939): Two Political Strategies”. Revue Française de Civilisation Britannique. French Journal of British Studies. XXVII (1). doi:10.4000/rfcb.8787. ISSN 0248-9015. S2CID 246524226. Archived from the original on 31 August 2023. Retrieved 31 August 2023.
- ^ “Global war’s colonial consequences”. academic.oup.com. Archived from the original on 31 August 2023. Retrieved 31 August 2023.
- ^ Dalrymple, William (22 June 2015). “The Mutual Genocide of Indian Partition”. The New Yorker. ISSN 0028-792X. Archived from the original on 23 April 2019. Retrieved 31 August 2023.
- ^ “How the Cold War Shaped Bangladesh’s Liberation War”. thediplomat.com. Retrieved 7 August 2024.
- ^ Foust, Joshua (16 December 2011). “No Great Game: The Story of Post-Cold War Powers in Central Asia”. The Atlantic. Retrieved 8 August 2024.
- ^ “Oil Discovered in Saudi Arabia”. education.nationalgeographic.org. Archived from the original on 3 December 2023. Retrieved 31 August 2023.
- ^ Bazelon, Emily (1 February 2024). “The Road to 1948, and the Roots of a Perpetual Conflict”. The New York Times. ISSN 0362-4331. Retrieved 8 August 2024.
- ^ “America’s Middle East Scorecard: Many Interventions, Few Successes”. NPR.
- ^ “Economic Issues 1 – Growth in East Asia”. imf.org. Archived from the original on 20 March 2023. Retrieved 31 August 2023.
- ^ “China’s Post-1978 Economic Development and Entry into the Global Trading System”. www.cato.org. Retrieved 9 August 2024.
- ^ Saul, Derek. “China And India Will Overtake U.S. Economically By 2075, Goldman Sachs Economists Say”. Forbes. Archived from the original on 5 July 2023. Retrieved 31 August 2023.
- ^ “25 years of liberalisation: A glimpse of India’s growth in 14 charts-Business News”. Firstpost. 7 July 2016. Archived from the original on 4 September 2023. Retrieved 4 September 2023.
- ^ Kumar, Manoj (17 July 2023). “One-tenth of India’s population escaped poverty in 5 years – government report”. Reuters. Archived from the original on 4 September 2023. Retrieved 4 September 2023.
- ^ Matamis, Joaquin (16 June 2024). “From the Mountains to the Seas: India-China Competition in the Wake of Galwan • Stimson Center”. Stimson Center. Retrieved 8 August 2024.
- ^ Kuo, Mercy A. “The Origin of ‘Indo-Pacific’ as Geopolitical Construct”. thediplomat.com. Retrieved 8 August 2024.
- ^ “A Map of the Countries between Constantinople and Calcutta: Including Turkey in Asia, Persia, Afghanistan and Turkestan”. Wdl.org. 1885. Archived from the original on 17 October 2017. Retrieved 9 November 2017.
- ^ “Asia”. Encyclopædia Britannica Online. Chicago: Encyclopædia Britannica, Inc. 2006. Archived from the original on 18 November 2008.
- ^ “Standard Country or Area Codes for Statistical Use (M49 Standard)”. UN Statistica Division. Archived from the original on 30 August 2017. Retrieved 2 May 2020. “Geographic Regions” anklicken Zitat: “The assignment of countries or areas to specific groupings is for statistical convenience and does not imply any assumption regarding political or other affiliation of countries or territories by the United Nations.”
- ^ Beck, Hylke E.; Zimmermann, Niklaus E.; McVicar, Tim R.; Vergopolan, Noemi; Berg, Alexis; Wood, Eric F. (30 October 2018). “Present and future Köppen-Geiger climate classification maps at 1-km resolution”. Scientific Data. 5: 180214. Bibcode:2018NatSD…580214B. doi:10.1038/sdata.2018.214. PMC 6207062. PMID 30375988.
- ^ “How melting glaciers contributed to floods in Pakistan”. NPR.org. Archived from the original on 9 September 2022. Retrieved 9 September 2022.
- ^ “Pakistan not to blame for climate crisis-fuelled flooding, says PM Shehbaz Sharif”. the Guardian. 31 August 2022. Archived from the original on 8 September 2022. Retrieved 9 September 2022.
- ^ Jump up to:a b c d e f g h i j k l m n o p q r Shaw, R., Y. Luo, T. S. Cheong, S. Abdul Halim, S. Chaturvedi, M. Hashizume, G. E. Insarov, Y. Ishikawa, M. Jafari, A. Kitoh, J. Pulhin, C. Singh, K. Vasant, and Z. Zhang, 2022: Chapter 10: Asia. In Climate Change 2022: Impacts, Adaptation and Vulnerability [H.-O. Pörtner, D. C. Roberts, M. Tignor, E. S. Poloczanska, K. Mintenbeck, A. Alegría, M. Craig, S. Langsdorf, S. Löschke, V. Möller, A. Okem, B. Rama (eds.)]. Cambridge University Press, Cambridge, United Kingdom and New York, New York, US, pp. 1457–1579 |doi=10.1017/9781009325844.012.
- ^ Armstrong McKay, David; Abrams, Jesse; Winkelmann, Ricarda; Sakschewski, Boris; Loriani, Sina; Fetzer, Ingo; Cornell, Sarah; Rockström, Johan; Staal, Arie; Lenton, Timothy (9 September 2022). “Exceeding 1.5°C global warming could trigger multiple climate tipping points”. Science. 377 (6611): eabn7950. doi:10.1126/science.abn7950. hdl:10871/131584. ISSN 0036-8075. PMID 36074831. S2CID 252161375.
- ^ Armstrong McKay, David (9 September 2022). “Exceeding 1.5°C global warming could trigger multiple climate tipping points – paper explainer”. climatetippingpoints.info. Retrieved 2 October 2022.
- ^ Kang, Suchul; Eltahir, Elfatih A. B. (31 July 2018). “North China Plain threatened by deadly heatwaves due to climate change and irrigation”. Nature Communications. 9 (1): 3528. Bibcode:2023NatCo..14.3528K. doi:10.1038/s41467-023-38906-7. PMC 10319847. PMID 37402712.
- ^ Jump up to:a b c d International Monetary Fund. “World Economic Outlook Database, April 2023”. International Monetary Fund. Archived from the original on 13 April 2023. Retrieved 7 May 2023.
- ^ “Largest_Economies_in_Asia”. Aneki.com. Archived from the original on 30 July 2022. Retrieved 9 November 2017.
- ^ “Hong Kong, Singapore, Tokyo World’s Top Office Destinations”. CFO innovation ASIA. Archived from the original on 7 August 2011. Retrieved 21 July 2011.
- ^ Farah, Paolo Davide (4 August 2006). Five Years of China WTO Membership: EU and US Perspectives About China’s Compliance With Transparency Commitments and the Transitional Review Mechanism. SSRN 916768.
- ^ Maddison, Angus (20 September 2007). Contours of the World Economy 1-2030 AD: Essays in Macro-Economic History. OUP Oxford. ISBN 978-0-19-164758-1. Archived from the original on 24 September 2020. Retrieved 30 May 2021.
- ^ Angus, Maddison (2003). Development Centre Studies the World Economy Historical Statistics: Historical Statistics. OECD. ISBN 978-9264104143. Archived from the original on 14 April 2021. Retrieved 30 May 2021.
- ^ Bairoch, Paul (1995). Economics and world history : Myths and paradoxes. University of Chicago Press. ISBN 978-0-226-03463-8.
- ^ “Table B–18. World GDP, 20 Countries and Regional Totals, 0–1998 A.D.” (PDF). theworldeconomy.org. Archived (PDF) from the original on 22 July 2013. Retrieved 20 September 2021.
- ^ Nalapat, M. D. (11 September 2001). “Ensuring China’s “Peaceful Rise””. Bharat-rakshak.com. Archived from the original on 10 January 2010. Retrieved 1 June 2010.
- ^ “The Real Great Leap Forward”. The Economist. 30 September 2004. Archived from the original on 27 December 2016. Retrieved 1 June 2010.
- ^ “Rise of Japan and 4 Asian Tigers from”. emergingdragon.com. Archived from the original on 22 April 2010. Retrieved 1 June 2010.
- ^ Fairless, Tom. “Rich Countries Are Becoming Addicted to Cheap Labor”. WSJ. Retrieved 4 June 2024.
- ^ “Global firms are eyeing Asian alternatives to Chinese manufacturing”. The Economist. Retrieved 4 June 2024.
- ^ “Philippine potential cited”. sme.com.ph. 24 February 2011. Archived from the original on 24 April 2011. Retrieved 1 March 2011.
- ^ “India growing as offshore outsourcing hub even for non-IT roles: Randstad India”. Business Today. 28 October 2021. Retrieved 4 June 2024.
- ^ “Melting Arctic ice could transform international shipping routes, study finds | Brown University”. www.brown.edu. 19 September 2024. Retrieved 20 November 2024.
- ^ “Estimated containerized cargo flows on major container trade routes in 2020, by trade route”. Archived from the original on 9 January 2021. Retrieved 26 January 2021.
- ^ “Global Marine Trends 2030 Report” (PDF). Archived (PDF) from the original on 12 April 2021. Retrieved 26 January 2021.
- ^ “Maritime Trade”. Archived from the original on 19 March 2021. Retrieved 26 January 2021.
- ^ Harry G. Broadman. “Afrika’s Silk Road” (2007), pp. 59.
- ^ Harry de Wilt. Is One Belt, One Road a China crisis for North Sea main ports? in World Cargo News, 17 December 2019.
- ^ Bernhard Simon: Can The New Silk Road Compete With The Maritime Silk Road? in The Maritime Executive, 1 January 2020.
- ^ Jean-Marc F. Blanchard “China’s Maritime Silk Road Initiative and South Asia” (2018).
- ^ “INTRA-ASIA”. Archived from the original on 26 January 2021. Retrieved 26 January 2021.
- ^ “Asia has more millionaires than Europe”. Toronto. Archived from the original on 25 June 2011.
- ^ Vallikappen, Sanat (28 March 2012). “Citigroup Study Shows Asian Rich Topping North American”. Bloomberg. Archived from the original on 14 January 2015.
- ^ World Bank’s GDP (Nominal) Data for Japan
- ^ World Bank’s GDP (Nominal) Data for Russia
- ^ World Bank’s GDP (Nominal) Data for Iran
- ^ “Peak GDP (PPP) for Turkey”. Retrieved 10 November 2024.
- ^ “Milan and Rome named among the most widely visited cities in the world in the Mastercard Global Destination Cities Index report”. Italianavenue.com. 28 May 2013. Archived from the original on 17 October 2017. Retrieved 9 November 2017.
- ^ Jump up to:a b c “2010 Human Development Report: Asian countries lead development progress over 40 years” (PDF). UNDP. Archived (PDF) from the original on 21 November 2010. Retrieved 22 December 2010.
- ^ Obeid, Anis (2006). The Druze & Their Faith in Tawhid. Syracuse University Press. p. 1. ISBN 978-0-8156-5257-1.
- ^ MacQueen, Benjamin (2013). An Introduction to Middle East Politics: Continuity, Change, Conflict and Co-operation. SAGE. p. 5. ISBN 978-1-4462-8976-1.
The Middle East is the cradle of the three monotheistic faiths of Judaism, Christianity and Islam.
- ^ Takacs, Sarolta (2015). The Modern World: Civilizations of Africa, Civilizations of Europe, Civilizations of the Americas, Civilizations of the Middle East and Southwest Asia, Civilizations of Asia and the Pacific. Routledge. p. 552. ISBN 978-1-317-45572-1.
- ^ “The Jewish Population of the World”. Jewishvirtuallibrary.org. Archived from the original on 21 June 2010. Retrieved 1 June 2010.
- ^ Ettinger, Yoram (5 April 2013). “Defying demographic projections”. Israel Hayom. Archived from the original on 29 October 2013. Retrieved 29 October 2013.
- ^ “Turkey Virtual Jewish History Tour | Jewish Virtual Library”. jewishvirtuallibrary.org. Archived from the original on 11 October 2014. Retrieved 15 December 2014.
- ^ “Ethnic composition of Azerbaijan 2009”. Pop-stat.mashke.org. 7 April 1971. Archived from the original on 7 February 2012. Retrieved 22 December 2012.
- ^ “Jewish woman brutally murdered in Iran over property dispute”. The Times of Israel. 28 November 2012. Archived from the original on 19 August 2014. Retrieved 16 August 2014.
A government census published earlier this year indicated there were a mere 8,756 Jews left in Iran
See Persian Jews#Iran - ^ “World Jewish Population 2007” (PDF). Archived from the original (PDF) on 26 March 2009. Retrieved 18 July 2015., American Jewish Yearbook, vol. 107 (2007), p. 592.
- ^ “World Jewish Population 2016 (DellaPergola, AJYB) | Berman Jewish DataBank”. jewishdatabank.org. Archived from the original on 30 September 2017. Retrieved 24 March 2018.
- ^ “Christians”. Pew Research Center’s Religion & Public Life Project. 18 December 2012. Archived from the original on 10 March 2015. Retrieved 13 March 2015.
- ^ Britannica Book of the Year 2014. Encyclopedia Britannica. 2014. ISBN 978-1-62513-171-3. Archived from the original on 29 April 2016. Retrieved 13 March 2015.
- ^ Jump up to:a b c d “Global Christianity – A Report on the Size and Distribution of the World’s Christian Population” (PDF). Pew Research Center. Archived (PDF) from the original on 9 August 2021. Retrieved 16 February 2022.
- ^ Hindson, Edward E.; Mitchell, Daniel R. (1 August 2013). The Popular Encyclopedia of Church History. Harvest House Publishers. p. 225. ISBN 978-0-7369-4807-4.
- ^ The Encyclopedia of Christianity, Volume 5 by Erwin Fahlbusch. Wm. B. Eerdmans Publishing. 2008, p. 285. ISBN 978-0-8028-2417-2.
- ^ “Region: Asia–Pacific”. Pewforum.org. 27 January 2011. Archived from the original on 10 October 2017. Retrieved 9 November 2017.
- ^ Colbert, C. Held (2008). Middle East Patterns: Places, People, and Politics. Routledge. p. 109. ISBN 978-0-429-96200-4.
Worldwide, they number 1 million or so, with about 45 to 50 percent in Syria, 35 to 40 percent in Lebanon, and less than 10 percent in Israel. Recently there has been a growing Druze diaspora.
- ^ Jha, Preeti (26 December 2007). “Guinness comes to east Delhi: Akshardham world’s largest Hindu temple”. The Indian Express. Archived from the original on 28 December 2007. Retrieved 2 January 2008.
- ^ “Cambodia”. The World Factbook (2025 ed.). Central Intelligence Agency. Retrieved 20 December 2010. (Archived 2010 edition.)
- ^ “Thailand”. The World Factbook (2025 ed.). Central Intelligence Agency. Retrieved 20 December 2010. (Archived 2010 edition.)
- ^ “burma”. The World Factbook (2025 ed.). Central Intelligence Agency. Retrieved 20 December 2010. (Archived 2010 edition.)
- ^ “Japan”. The World Factbook (2025 ed.). Central Intelligence Agency. Retrieved 20 December 2010. (Archived 2010 edition.)
- ^ “Bhutan”. The World Factbook (2025 ed.). Central Intelligence Agency. Retrieved 20 December 2010. (Archived 2010 edition.)
- ^ “The Census of Population and Housing of Sri Lanka-2011”. Department of Census and Statistics. Archived from the original on 24 July 2013. Retrieved 29 July 2013.
- ^ “Laos”. The World Factbook (2025 ed.). Central Intelligence Agency. Retrieved 20 December 2010. (Archived 2010 edition.)
- ^ “Mongolia”. The World Factbook (2025 ed.). Central Intelligence Agency. Retrieved 20 December 2010. (Archived 2010 edition.)
- ^ “Taiwan”. The World Factbook (2025 ed.). Central Intelligence Agency. Retrieved 20 December 2010. (Archived 2010 edition.)
- ^ “China (includes Taiwan only): International Religious Freedom Report 2005”. US Department of State: Bureau of Democracy, Human Rights, and Labor. 8 November 2005. Archived from the original on 26 December 2020. Retrieved 24 January 2008.
- ^ “China (includes Taiwan only): International Religious Freedom Report 2006”. US Department of State: Bureau of Democracy, Human Rights, and Labor. 15 September 2006. Archived from the original on 17 September 2020. Retrieved 24 February 2008.
- ^ “China (includes Taiwan only): International Religious Freedom Report 2007”. US Department of State: Bureau of Democracy, Human Rights, and Labor. 15 September 2006. Archived from the original on 25 June 2020. Retrieved 24 February 2008.
- ^ “South Korea”. The World Factbook (2025 ed.). Central Intelligence Agency. Retrieved 20 December 2010. (Archived 2010 edition.)
- ^ “Malaysia”. The World Factbook (2025 ed.). Central Intelligence Agency. Retrieved 20 December 2010. (Archived 2010 edition.)
- ^ “Nepal”. The World Factbook (2025 ed.). Central Intelligence Agency. Retrieved 20 December 2010. (Archived 2010 edition.)
- ^ “vietnam”. The World Factbook (2025 ed.). Central Intelligence Agency. Retrieved 20 December 2010. (Archived 2010 edition.)
- ^ “Chinese Han Nationality: Language, Religion, Customs”. Travelchinaguide.com. Archived from the original on 17 October 2017. Retrieved 9 November 2017.
- ^ “Culture of North Korea – Alternative name, History and ethnic relations”. Countries and Their Cultures. Advameg Inc. Archived from the original on 5 August 2009. Retrieved 4 July 2009.
- ^ “North Korea”. The World Factbook (2025 ed.). Central Intelligence Agency. Retrieved 9 November 2017. (Archived 2017 edition.)
- ^ Bureau of East Asian and Pacific Affairs (2009). “Background Note: North Korea”. U.S. State Department. Archived from the original on 18 August 2020. Retrieved 4 July 2009.
- ^ “Geographic Regions”. United Nations. Archived from the original on 30 August 2017. Retrieved 31 March 2018.
- ^ Collon, Dominique. “BBC – History – Ancient History in depth: Mesopotamia”. Archived from the original on 2 January 2023. Retrieved 31 March 2018.
- ^ Morris, Ian (2011). Why the West rules – for now : the patterns of history, and what they reveal about the future. Profile. ISBN 978-1846682087. OCLC 751789199.
- ^ Lockard, Craig A. (19 June 2014). Societies, Networks, and Transitions, Volume I: To 1500: A Global History. Cengage Learning. ISBN 978-1285783086. Archived from the original on 26 March 2023. Retrieved 31 March 2018.
- ^ “Muhammad Yunus returns to Bangladesh to lead interim government”. Al Jazeera. Retrieved 11 September 2024.
- ^ His Holiness’s Teachings at TCV. “A Brief Biography – The Office of His Holiness The Dalai Lama”. Dalailama.com. Archived from the original on 25 May 2010. Retrieved 1 June 2010.
- ^ “Democracy Report 2024, Varieties of Democracy” (PDF). Archived (PDF) from the original on 12 March 2024. Retrieved 16 March 2024.